The Ducerf Group's action plan to triple it’s internal supplies by 2027 includes both development potential and purchasing tensions.
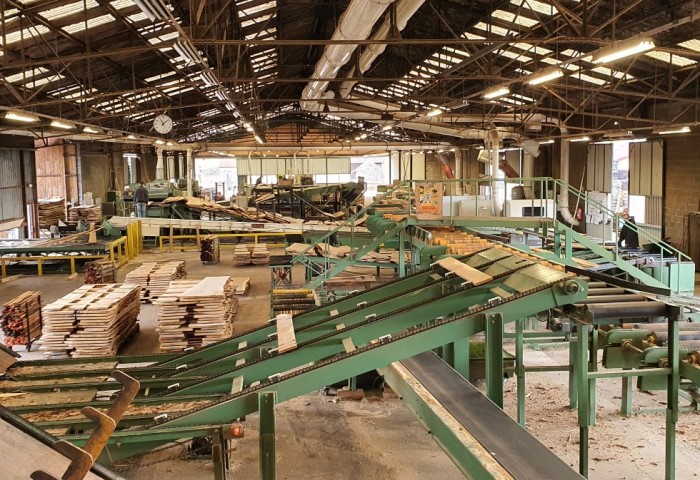
Secure the materials, maintain product quality, and be flexible! Faced with recent crises, the Ducerf Group adjusts to various needs and makes significant investments. How are we going to accomplish this? By advancing the industrial tool's modernization. The action plan defined clear objectives: digitalisation, automation, and a new transformation line. "By 2027, half of the wood used at our secondary transformation sites will have come directly from our Burgundy sawmill, compared to 15% now." This bold option will enable us to further secure the Group's supplies in a situation of exceptional purchasing tensions, thanks to the development of the internal resource, its optimization, and the increase in production capacity. And create the groundwork for the sawmill of the future."
It all began with a simple observation. "Today, 85 percent of the wood we use for secondary processing for finger-jointed products comes from our historical suppliers, partner sawmills," says Ducerf Group CEO Edouard Ducerf. Despite the fact that this is our family's core business, the French network of primary processing enterprises is dwindling year after year. In a time of high demand, our efforts to secure supply have taken on even more significance. Indeed, the number of sawmills in France has been divided by ten since 1960: according to the Ministry of Agriculture, there were 1,308 sawmills in France at the end of 2020. Every year, roughly 50 businesses close due to a lack of buyers or appropriate investment.
"What is our goal?" To enhance our proportion of internal supply and thereby achieve our development goals by accelerating the integration of first and second transformation processes. "
"The sector is regarded unattractive by potential investors due to the requirement to bring in a large amount of capital and the sector's relatively low profitability, and sawmills continue to decline." Simultaneously, there is a concentration of remaining actors in the wood sector, who only absorb a portion of the wood volumes from these vanished structures, with the remainder escaping national production." "In other words, the products required for our second transformation, these small bits of wood generated by sawmills that we valorize by finger-jointing, are lacking in favor of export," Edouard Ducerf says. To attain our goals, we must reorganize ourselves in light of this fact and modernize our production equipment. Because the Group's long-term survival is on the line.
Renowned for its know-how and its ability to store material, the Group is now working to secure its supplies of wood for secondary processing, whether for glued laminated panels and strips, solid wood, decking and cladding or wooden decking. "Market demand is strong and it is essential for us to be able to meet all needs, in terms of volume, quality and the types of wood species required," says the CEO. "It is therefore a real added value for the Ducerf Group to control the entire production chain in France. It is a strong commitment to our independence. Because securing our supplies means securing our customers' supplies. This is a point of honour that we make as a reliable supplier. However, there is no question of cutting ourselves off from our current suppliers. "They are valuable, we are very attached to these partners and our relationship will continue. Our strategy is simply to increase our volumes from the group in order to achieve our development objectives.
"Having an integrated business logic is the key to sustainability."
To do this, the experienced teams of log buyers are strengthening their cooperation with the upstream forestry sector: private or institutional forest owners, companies and cooperatives. "It's a necessity," says Jean-Marie Ducerf, the group's industrial director. "We note that part of the forest is still insufficiently exploited and developed, for example certain species such as beech or chestnut, or part of the resource that is currently only used as energy wood. In the future, the idea is to have the capacity to process them to obtain products with higher added value and more remuneration for the forestry sector, while creating more value in our production chain.
The underlying theme is responsiveness. "By directing our traditional sawmill towards more manufactured products to bring them more value, we will be responding to an increasingly important need from industrialists in the wood sector," explains Thibault Chastagnier, head of the secondary processing division. "Moreover, integrating the supply of secondary processing units will automatically lead to time savings and an increase in our reactivity, where our customers expect tailor-made solutions and a high degree of flexibility on our part. It is this reactivity that often makes the difference, alongside quality and price," he notes. And Edouard Ducerf adds: "The sawmill of the future is being designed today in a context of major tensions on the material and supply difficulties. Our stock level is already a strong point to overcome the problem. But having an integrated operational logic in parallel will be the key to endure!
Sawmill of the future: the strategic steps of the action plan
Our ambition is therefore to accelerate our development to meet these vital challenges. To secure our supplies, control the high quality of our products and develop new ones, our intentions are clear: "We aim to increase our capacity to supply our secondary processing sites internally by at least a factor of 3 within the next 3 years", says Edouard Ducerf, "In concrete terms, this means that by 2027, not 15% but 50% of secondary processing production, mainly in oak, will come from our Burgundy sawmills. We may have to diversify further by increasing the volume of sawn timber from other species such as beech or ash for example.
And this is our action plan to achieve this.
Phase 1 : Deployment of a new processing line
Modernising the production facilities at the sawmill site is essential. And we are doing everything we can to do so! And how? With a dedicated tool.
This new machine will be used to make items for secondary processing, such as finger-jointed wood. "To do this, connected and predictive 4.0 technologies like scanners will be incorporated," says Benoît Besseau, a research and development engineer at the Ducerf Group who recently completed a thesis on the topic.
What is the goal? To achieve high production rates while maintaining optimal material sorting quality and expanding our flexibility to satisfy specific and timely tailor-made requirements.
The Ducerf Group is very attached to the material it transforms and tries to optimize it as much as possible. This is also part of a larger strategy to improve the value of secondary quality oaks and the development of new wood products, particularly for the construction industry.
Phase 2 : 20% increase in secondary processing capacity
We'll step it up a level as soon as the sawmill is able to service the secondary processing sector on a greater scale! As a result, increasing our manufacturing capacity will go hand in hand with reorganizing the tool.
With the goal of increasing productivity, investments in existing lines and new equipment are planned.
The diversification of the species processed will also be a determining factor. "Because today, a quarter of the volumes absorbed in secondary processing are not oak, which is far from negligible," recalls Thibault Chastagnier. "The overall modernisation of our tools will enable us to increase these shares to meet the needs of the market.
The result? The volumes processed in secondary transformation will increase by 20% over the period, while being secured upstream by the developments of the Ducerf sawmill. The circle will be closed!
Improved working conditions, positive environmental impact... The virtuous circle of the committed approach
"It is the natural consequence of the modernization of our industrial tool: new jobs will be created, accompanied by an increase in the skills of the internal teams", Jean-Marie Ducerf enthuses. Less drudgery, more comfort, strong support... Working conditions will also improve. "We are going to be even more attractive for all these jobs, with an increased need for qualified personnel. Training will be a major issue," he explains.
Another notable benefit of this strategy of securing supplies and controlling product quality is the resulting environmental impact. In secondary processing, our suppliers are located within an average radius of 270 kilometres from our production sites," explains Thibault Chastagnier. Tomorrow, with 50% of the volume passing through the sawmill coming from neighbouring regions, the impact of transport will be considerably reduced.
A visionary strategy
Furthermore, when processing volumes increase, more associated products, including as short offcuts, sawdust, chips, and bark, will be produced. Their recuperation, which is critical, will also allow for the provision of greener energy. "This provides up fantastic development opportunities while also emphasizing our optimistic attitude," Edouard Ducerf says.
The family business continues to adapt as a visionary. In the face of a shifting economic climate, the Ducerf Group once again demonstrates its ability to innovate and make significant investments. This proposal is both ambitious and feasible, as it aims to triple internal supply in five years. "It ensures the quality of our products, as well as our independence and the independence of our customers." It's a strategy that addresses both the wood industry's difficulties and the new outlets that are emerging today. And action!
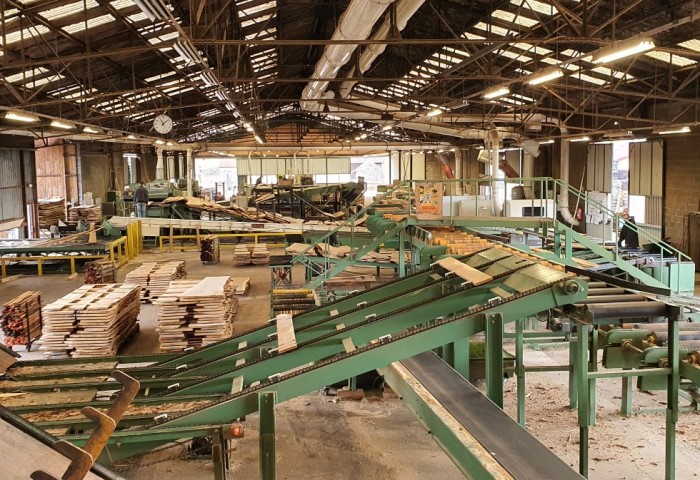
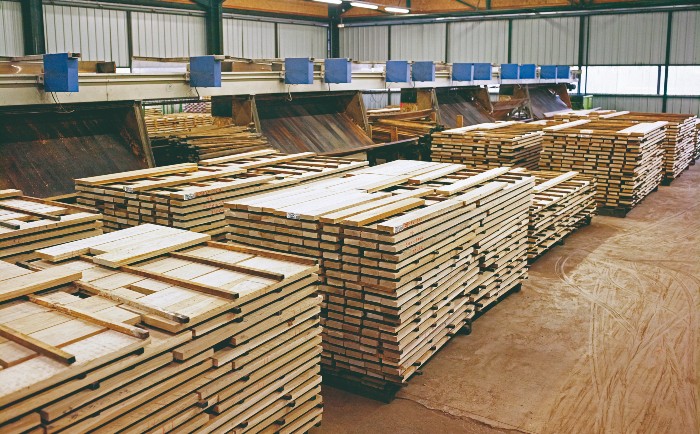
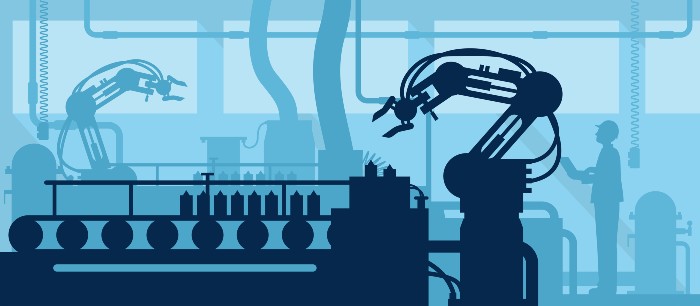
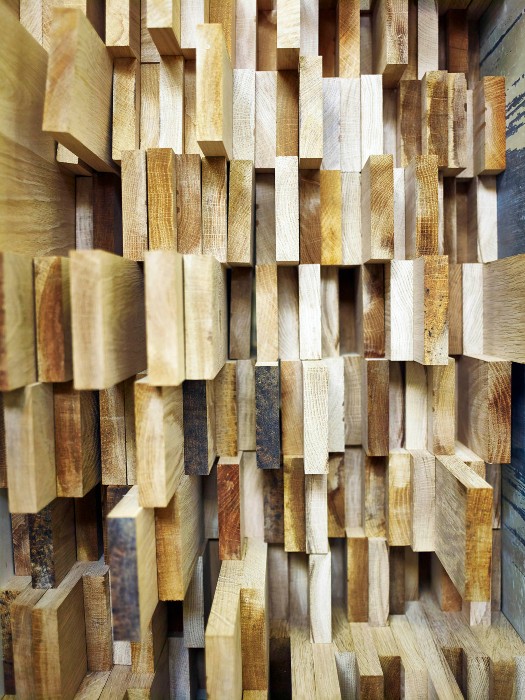
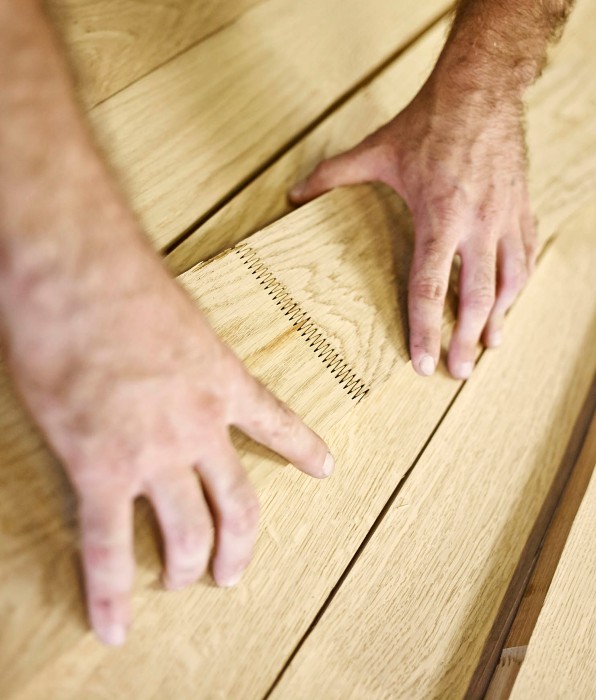
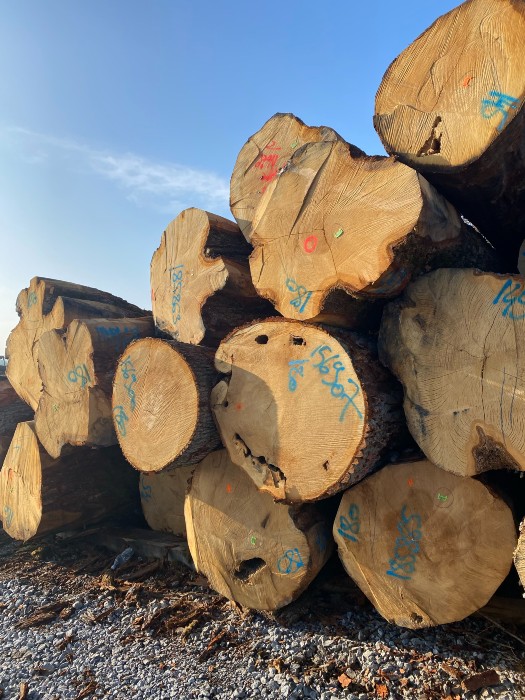
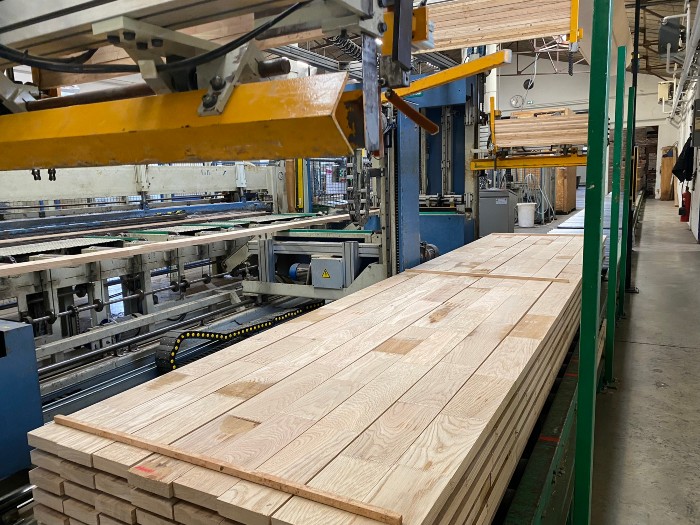