A new high-frequency press, Groupe Ducerf accelerates its transformation
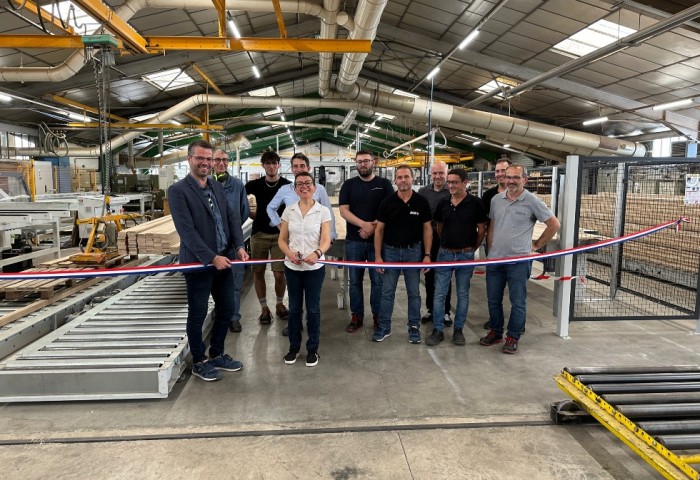
Groupe Ducerf invested €1.7 million in a cutting-edge high-frequency press. This ultra-modern, 4-in-1 piece of equipment expands the range and formats of our products. Thanks to this new machine, developed in collaboration with Weinig, our solid wood panels Panoplot®, glued-laminated panels Patchwood®, joinery blocks, and the first elements of future oak CLT (Cross-Laminated Timber) panels are now being manufactured. This innovation significantly improves resource management and enhances the working conditions of our operators.
Since summer 2024, Groupe Ducerf has entered a new era. With the installation of a high-frequency press at the Bois Profilés site in Charolles (71) for a €1.7 million investment, our family-owned company now boasts breakthrough technology.
"For several years, we’ve identified our main growth limitation as our gluing capacity," explains Julien Guenard, head of the Second Transformation division. "We were reaching saturation. On some production lines, we operated 24/7. The idea behind this investment is to introduce flexibility, expand our development capacities, enhance the quality of our gluing processes, and open new horizons."
A crucial investment for the present and future
This investment is vital for the Burgundy-based group, both now and in the years to come. "If we want to continue offering French-made engineered wood products, modernization is essential," notes Thibault Chastagnier, Technical Director of Groupe Ducerf. "We need state-of-the-art tools to improve productivity and optimize material yield. Today, we have a system that can produce four different products on one line, with varying formats—whether for joinery blocks, solid panels (Panoplot®), glued-laminated panels (Patchwood®), or the future plies of our oak CLT. This enables us to market high-quality, affordable construction materials."
"Four products, with panels up to six meters long"
This machine, co-designed with German company Weinig, is 50 meters long and 10 meters wide. It is now the largest production line in the group’s Second Transformation division. Replacing three old cold presses, this high-frequency technology enables much faster gluing cycles.
Its operating principle involves running an electric current between the upper and lower plates through the glue joint, which primarily consists of water. This heats the glue joint, accelerating polymerization. The result? High-quality gluing in record time.
Additionally, "this press allows us to expand the Patchwood panel offering," says Julien Guenard. "It meets customer demand for optimized cuts with minimal waste. We can now produce panels 6 meters long, 120 cm wide, and 10 cm thick. For Panoplot, it primarily expands our width ranges and supports custom production, as we recently did for our client Bastiat, who manufactures chairs for Notre-Dame. For the joinery block range, we can work twice as fast, offering more flexibility and responsiveness to our clients. Finally, in Burgundy, we’re initiating oak CLT wall production, and this press will supply large-format semi-finished panel elements, facilitating the creation of cross-laminated panels."
"Minimizing material waste"
This investment reflects Groupe Ducerf’s commitment to French production and local wood industries.
"We’re seeing growing enthusiasm for French wood products," says Thibault Chastagnier. "This national sourcing strategy has become a priority for clients—both distributors and manufacturers. As a key player in this field, we had to align with this market by investing to address future challenges."
This modernization also optimizes resource management. "The press allows us to glue longer slats, made from edged boards and finger-jointed strips, which are related products of sawmills," explains Julien Guenard. "Finger-jointed solid wood is our expertise, and now we can use secondary-quality oak for CLT panels, maximizing the value of an underutilized resource."
Moreover, glue consumption is reduced. "The precision of glue application significantly limits waste. The grammage is more accurate and consistent, and cleaning is much simpler."
"Transforming working conditions"
Another major advantage of this new press is its impact on operator working conditions. "With this next-generation tool, we have fewer bad postures and reduced strain because everything is done at working height," explains Dominique Chapuis, a press operator. "Now, we focus more on monitoring than manual handling. It completely changes our working conditions—no more back pain, less fatigue, and we go home feeling better. There’s also pride in working with advanced technology and gaining new skills."
Part of this investment was financially supported by CARSAT BFC through a professional risk prevention contract. Operators were actively involved in the project, from visiting similar machines to contributing to the specifications and supplier selection.
"This investment was built with our teams, which makes it virtuous," emphasizes Thibault Chastagnier.
Laying the Foundation for the Future
This significant investment sets the stage for Groupe Ducerf’s future, emphasizing humanity, productivity, creativity, and sustainability. "This is the first step in our reindustrialization project," adds Thibault Chastagnier. "A machine capable of 4-in-1 gluing didn’t exist before. It symbolizes Groupe Ducerf’s core values: people at the center, technology, innovation, and client service!"
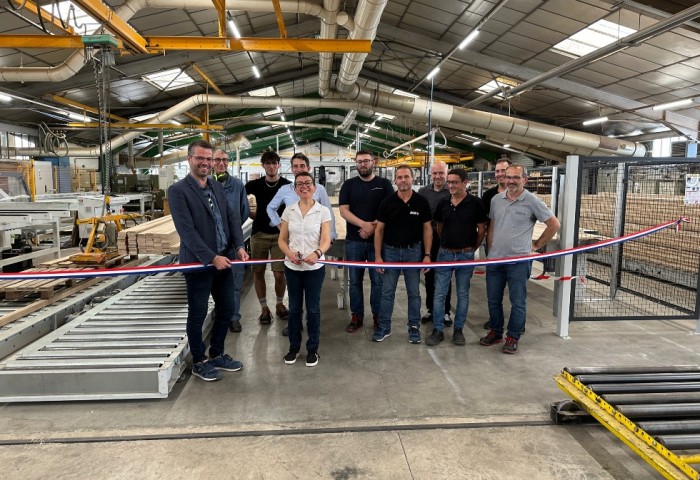