Let’s discover the professions at the Ducerf sawmill!
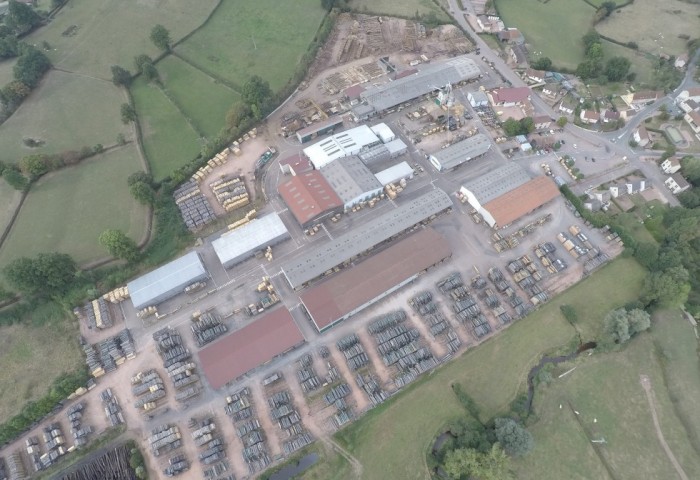
The sawmill at Vendenesse-lès-Charolles (71), one of the group’s 3 manufacturing sites, is a key location for Ducerf’s activity. This is where a large part of our 50,000 m3 of logs are transformed each year. Timber volumes that need to be sorted, stored and sawed according to their quality and their intended use. Thanks to strict manufacturing controls and the diligence of each of our teams, our clients are ensured products of superior quality. The secret behind this success: experienced and highly skilled workers who take pride in their mission. Encounters…
That everyone is where they are supposed to be
Jean-Marc Cauvas, Manager of the sawmill: “Jean-Marie Ducerf, Sébastien Grisard and myself manage this site together. Our role is to organise production on a daily basis and to supervise the teams. These are comprised of about twenty individuals on rolling shifts of 11 hours per day. In this position, it’s important to know exactly how to put the skills of each individual to use in the right place, both for their own well-being and so that we can fulfil our production objectives. The maximum capacity of the different sites in covered stock is 25,000 m² and at Vendenesse-lès-Charolles we work on these stocks in order to unfailingly satisfy customer demand. We saw around 150 m3 per day, which makes approximately 14 m3 per hour. Over a year, multiply that by about 220 working days and you can get an idea of our yield! ”
Know the forest to better guide the logs
Arnaud Cognard, logs supervisor: “I’m the first link in the production chain! My role is to take log deliveries arriving from the forests into the logyard, to grade them depending on their quality and their diameter, and to dispatch them to the sawmill according to demand. It’s all the more important given the current cost of timber. So it’s necessary to have knowledge of standing trees and to know their uses. To that end, I continue to go to the forest and to have a strong relationship with the forestry team. I’ve been with the company for 19 years now, and as it’s a key position, it’s fairly rewarding. The only real constraint is that involves working outside all year round, but that’s the job, and anyway I love it! ”
Always have the perfect cutting tool
Ludovic Conti and Gilbert Momesin, sharpening supervisors:
Ludovic Conti: “For us, the idea is to make sure that we provide the perfect cutting tool, because even the best sawyer in the world wouldn’t be able to cut straight if that wasn’t the case! So, when sharpening, we carry out precision work to the 10th or even 100th of a millimetre, using sophisticated machines that are digitally controlled. It’s a profession that requires great concentration, technical knowledge and precision in what we do. Our mission combines work on the factory floor and operations in the sawmill. It involves maintenance, the changing of blades or of different irons, knives. But our main activity involves the preparation of double-cut bandsaws. This is also the most high-precision task we perform. The main constraint here is obviously compliance with safety regulations because these are extremely sharp cutting objects that are handled from morning to night, so there is absolutely no room for error. ”
Gilbert Momesin: “I’ve been working for the Ducerf group for 41 years, a good deal of that at sharpening. And in 25 years, the job has changed enormously. In the past, we used single-edged blades, nowadays we use double-cuts. It’s more modern and production has increased as a result, but it’s also necessary to be that much more accurate. Every 4 hours, we change the blades and carry out revision: levelling, tensioning and sharpening. Our obsession is to make sure that there are absolutely no bumps on the blade, as these would skew the cut and product quality would suffer as a result. ”
That the machine never stops
Anthony Turret, Head of maintenance: “My primary task is to ensure that there are as few as possible interruptions to production. For this, I’m in charge of all stock management, in order to supply as quickly as possible, while carrying out investments for the set-up of machines and organising the different interventions of maintenance technicians. This requires forward planning of the steps involved in summer or winter revision works. And at the same time, it’s my job to continuously improve safety and working conditions for each workstation. I particularly enjoy the familiar atmosphere in this company, where everybody knows each other, and also that I’ve been given responsibilities, despite the fact that I’m still young. It’s very rewarding. ”
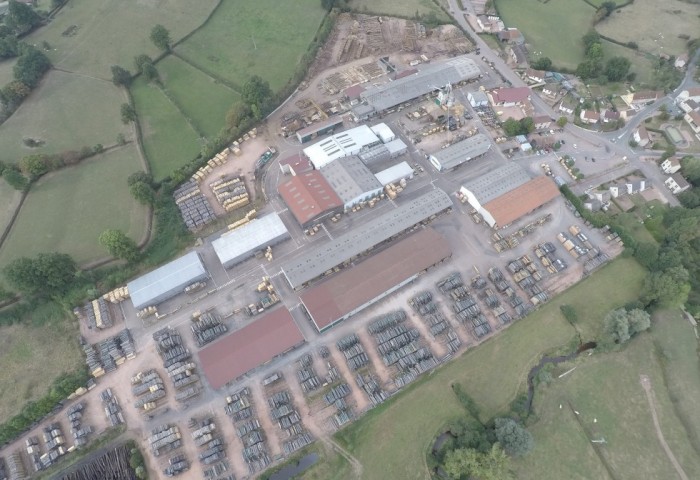



