Ducerf Group Design Office: listening, advice and co-design as drivers of successful projects!
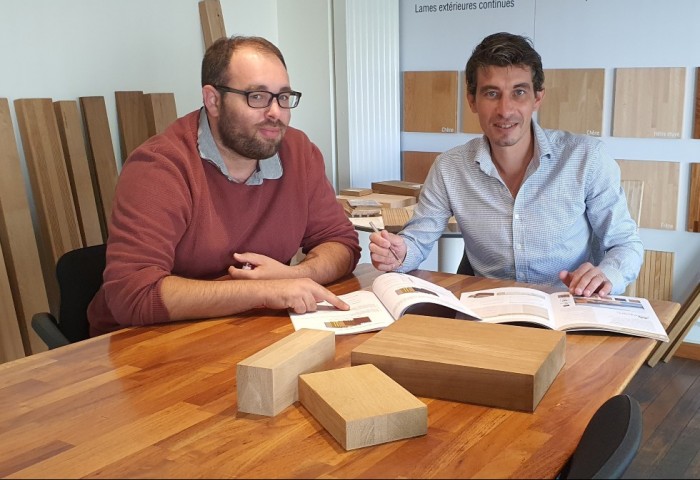
To best meet its clients’ needs the Ducerf group relies on the quality of its products, but it also listens attentively to its customers. The purpose of the design office is to provide the most appropriate solutions for different projects from the technical, regulatory and financial points of view. We met up with two of the key protagonists: Thibault Chastagnier, Manager of the secondary processing division, and Julien Guénard, Production Manager in the secondary processing division…
What is the role of the design office at the Ducerf group?
Thibault Chastagnier: It has a pivotal role in that it pulls together the skills, experience and know-how of the group’s various actors. Members of the design office are usually consulted by the sales teams, depending on the complexity of projects. I am involved as Manager of the secondary wood processing division. I contribute my knowledge for projects that involve building work, as well as for monitoring standards and collaborative programmes. Alongside me, Julien Guénard, the Production Manager, is in charge of optimising wood processing, raw materials and production costs. Then we have the workshop foremen who decide if something is feasible or not. This is an important process because our customers expect to receive technical expertise.
Which customers most require this type of technical support?
Thibault Chastagnier: We often become involved at a very early stage alongside the general contractor, the architect, the design office and the installation company. We receive a lot of requests during the implementation phase, these usually involve clients of the exterior product range. And then there are the manufacturers, managed by Julien. In this case we often get involved in co-development with the customer.
Julien Guénard: In fact, large industrial organisations generally have their own design offices. They conceptualise and develop products, transfer them to us and we then look at how manufacturing processes can be adapted. We design the product together and assist them by looking for the best solution in terms of quality and price. The manufacturer defines the initial requirements and we work together to achieve them.
“Seeking compromise and guiding the customer towards the most appropriate solution”
How exactly do you go about advising professionals who come to you for expertise?
Thibault Chastagnier: We work on a case by case basis. The idea is to understand the end-customer’s need, from the woodworker to the manufacturer. We examine the availability of raw materials, the grades of lumber required, and we work on the design, providing advice and making sure the product is stable.
Julien Guénard: This consulting phase is crucial. At times we actually steer the customer towards an alternative strategy to the one initially planned as technical feasibility may not always be confirmed. Depending on what our assessments reveal in terms of restrictions, we may suggest optimised alternative solutions which are close to the initial requirements. It’s a genuine partnership that benefits the various stakeholders, we make compromises but always conforming to the project plans.
Are the co-design and co-development of new products essential aspects of the design office’s work?
Thibault Chastagnier: Yes, and there are two specific cases. First of all, there are products that we develop according to customer specifications. This involves the development of products in conjunction with the manufacturer. For instance, they design a new product range and want to fine-tune each component. In this case the customer expects us to make suggestions and may also require our help in optimising the materials: performance, quality, properties, price. Co-design is an approach that creates genuine partnerships and lasting commitments with our customer. It’s a win-win situation. Sometimes we co-design certain aspects with the architect, as was recently the case for a specific request. For Amiens Zoo we were asked to provide cladding that resembled animal scales. We are conduct feasibility and optimisation studies based on current production capacities, potential investments to be made and the outsourcing of certain operations.
“One of the main challenges: optimising materials to the fullest while remaining cost effective”
In the second case, the Ducerf group team actually designs the products itself...
Thibault Chastagnier: More precisely, we develop our own products to respond to needs identified by the Ducerf group. Feedback on consumer needs and market trends comes from our sales teams for the most part. The innovation and marketing committee may then sense an opportunity and draft a project for the R&D department (to cite a few examples: oak panels with HDF cladding, special oak boards for scantlings, and cambered decking). It may also concern a raw materials resource. We might, for instance, be interested in chestnut. It's a material which is easy to find and has properties close to those of oak, but a little less expensive. It’s a regional market that could become more widespread. Designs can also arise from encounters, as was the case with the designer Sylvain Hardy and the development of his YD-Woods graphic panels. These requests are handled by the design office to enable technical and economic studies to be carried out and presented to the innovation and marketing committee. Based on this data, the innovation and marketing committee provides further feedback, we then move on to the prototyping phase. Once approved, the project proceeds to the manufacturing phase.
Rigorous efforts to satisfy regulatory requirements and standards.
In terms of regulations and standards, what does the design office do to meet the requirements?Thibault Chastagnier: The requirements vary widely depending on the types of products. For interior design and decoration there are few restrictions, although over the last few years we’ve seen the emergence of certifications enabling us to label products according to their environmental impact. As such, our ranges of panels have been awarded the green label (Excell). Outdoor products (the Côtéparc range) such as cladding thermotreated and decking are intended for constructors, as the regulatory framework is fairly complex. We monitor the regulations and their evolution closely. These two product families carry the CE mark. Requirements also differ between public and private markets, depending on the type of building and the restrictions relating to fire prevention. We are able to adapt projects by providing the most suitable solutions, one example being the intumescent treatment we apply to our products and which we have continued to develop over recent years. They are excellent solutions for enabling wood to be used in projects with complex requirements.
And which products does CTB-Lca certification apply to?
Julien Guénard: This certification is for products types such as solid wood, glulam, finger-jointed scantlings. It applies to all products we use for interior and exterior joinery fittings. This is a heavily standardised sector. Door and window manufacturers have a number of certifications / charters such as “NF fenêtres” and “Menuiserie 21”. These specifications stipulate that scantlings and glulam components must come from certified suppliers. The certification process guarantees that the glue performs correctly. Too obtain this certification, the design office needs to ensure that we comply with specifications through audits, sampling campaigns, delamination tests and production controls. For us, CTB-Lca certification is essential because it is a market requirement.
"Encouraging wholesalers, woodworkers and architects to come to us for advice on the use of products."
Following on from design work and the choice of materials, you are also involved at the implementation stage...
Thibault Chastagnier: Yes, and it’s a service that’s not widely known about. Yet today, the majority of legal disputes involve inappropriate implementation. If we know the intended use of products before we sell them, we can recommend the correct installation method. With this in mind, the group is doing the groundwork with wholesalers by giving presentations of products to joiners in focused meetings led by sales staff, involving the optimisation of plans, sampling, test phases, etc.
In illustrating the bespoke creations with which the design office is involved, which representative projects come to mind?
Thibault Chastagnier: We could mention the project for the SNCF footbridge in Laval, or the Sports Complex in Boulogne-Billancourt. We were in charge of the laying out process for the façades to optimise the use of materials. On each occasion our design office was able to improve on the design of the architect’s initial project and lift major technical blocks, while remaining perfectly in line with the philosophy of the projects themselves. These services are truly appreciated by our customers and are a source of pride for the group!
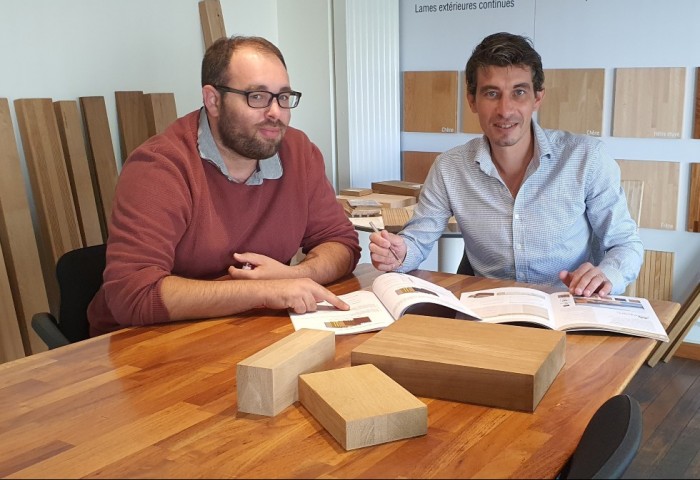





